When choosing heat sink for yourself, there are several factors you should consider among which the key one is the material types of heat sink. In this post, we will discuss anodized heat sinks and answer some questions that people are always concerned about.
What is the coating of heatsinks?
Heat sink coating is the corrosion resistance and scratch resistant of the external layer including anodizing, passivation and chrome plating, and so on. Anodizing is one of the most common processes for manufacturing aluminum heat sink. The heatsink is immersed in the anodizing tank with chromic acid or sulfuric acid, which forms an oxide film of 5-25um thickness on the aluminum surface that is resistant to wear and corrosion. Currently, the common colors of oxide coatings are black, blue, and brown, but you can also customize heat sink to achieve a different appearance. These coated heatsinks are generally used for electronic equipment, or internal combustion engines to ensure their smooth operation.

Does the color of a heatsink matter?
In natural convection, a black or dark-colored heatsink will perform 3% to 8% better than a natural silver-colored one, as the fact that dark colors radiate heat more efficiently. However, compared to passive heat dissipation, the heatsink color barely stands its ground anymore. Adversely, the size, thickness, and surface area are the key factors affecting thermal conductivity. In general, the current oxidation color mainly plays a role in corrosion protection and aesthetics.
What is the 720 rule for anodized parts?
The 720 rule describes the relationship between the amount of electrical current and the thickness of the anodizing layer produced over time inside original aluminum. It is known that anodized layer with thickness ranging from 0.001 or 25.4 microns per square foot requires 720 A/min. By the 720 rule, the surface finish can be better controlled for matching power of electronic devices.
Is anodizng heat resistant?
Anodizing is a safe process that is not harmful to human health. An anodized finish is chemically stable, will not decompose; is non-toxic; and is heat-resistant to the melting point of aluminum (1,221 degrees F.)
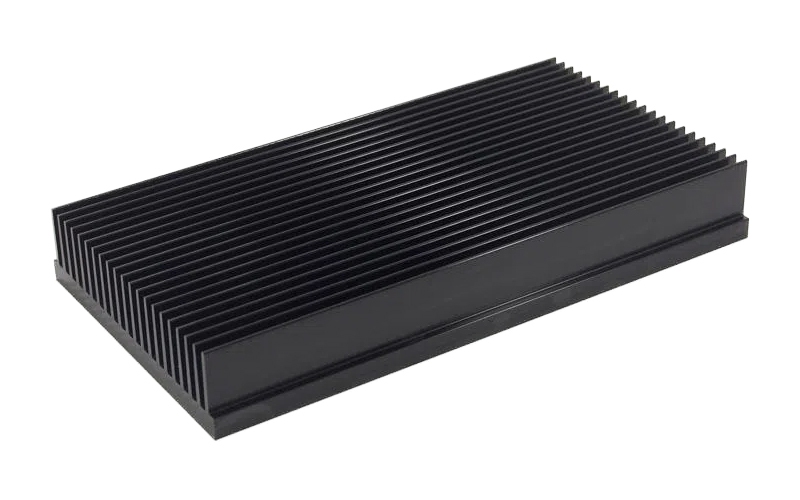
Does anodizing aluminum wear off?
It has been proven that the oxide film cannot be scraped off from the surface, because the chemicals penetrate from the surface into the anodized aluminum part. Therefore, the only way to remove the aluminum surface treatment is by grinding off the aluminum substrate, which also demonstrates the outstanding performance of anodized aluminum.
How does heat affect anodized aluminum heat sink?
Anodized aluminum heat sinks are known to be effective in transferring heat from one electronic device to another. However, when subjected to extreme temperature differences, anodized aluminum parts will crack. Therefore, when using anodized aluminum radiators, you should keep the temperature below about 185°C to prevent damage from overheating. The reason for this is that thermal expansion coefficient of bare aluminum is 5 times greater than that of anodized aluminum, which can cause cracks to form when subjected to heat.

Is anodizing permanent?
Anodizing aluminum parts has many benefits in aesthetics and mechanical properties. Visually, it is quite impressive, and the finish is permanent. On top of that, it is wear-resistant, meaning that it will never scratch or fade and will never need to be touched up.
Is anodizing thermally conductive?
Thermal conductivity is determined by the heat flow, the thickness of the material, and the surface area of specific alloy. Anodizing creates an additional oxide layer (anodized surface) on the surface of the aluminum part, which increases the thickness and surface area of the part. As a result, the thermal conductivity of anodized aluminum is improved compared to unfinished aluminum parts. This makes anodized aluminum parts ideal for heat sinks in today’s electronics and other thermal systems.
What is the difference between Type 1 and Type 2 anodizing process
There are three types of aluminum anodizing process: Type i is chromic acid oxidation for producing a dense coating. The oxide coating (typically 2.5 microns) is suitable for applications with low corrosion conservation and paint adhesion; Type ii uses a sulfuric acid mist to form a dense oxide layer (typically 25 microns) on the aluminum heatsink. Due to the thicker anodic coatings and porosity, the latter retains the surface coloration better than Type i aluminum part. In terms of price, however, Type 2 is more expensive for which the anodizing process will be much more complex than primary anodizing. In addition, Known as Type iii anodizing, it also calls hard coat anodizing, which does further oxidation based on type ii anodizing to increase wear resistance, which results in a thicker oxide layer (>25 microns).
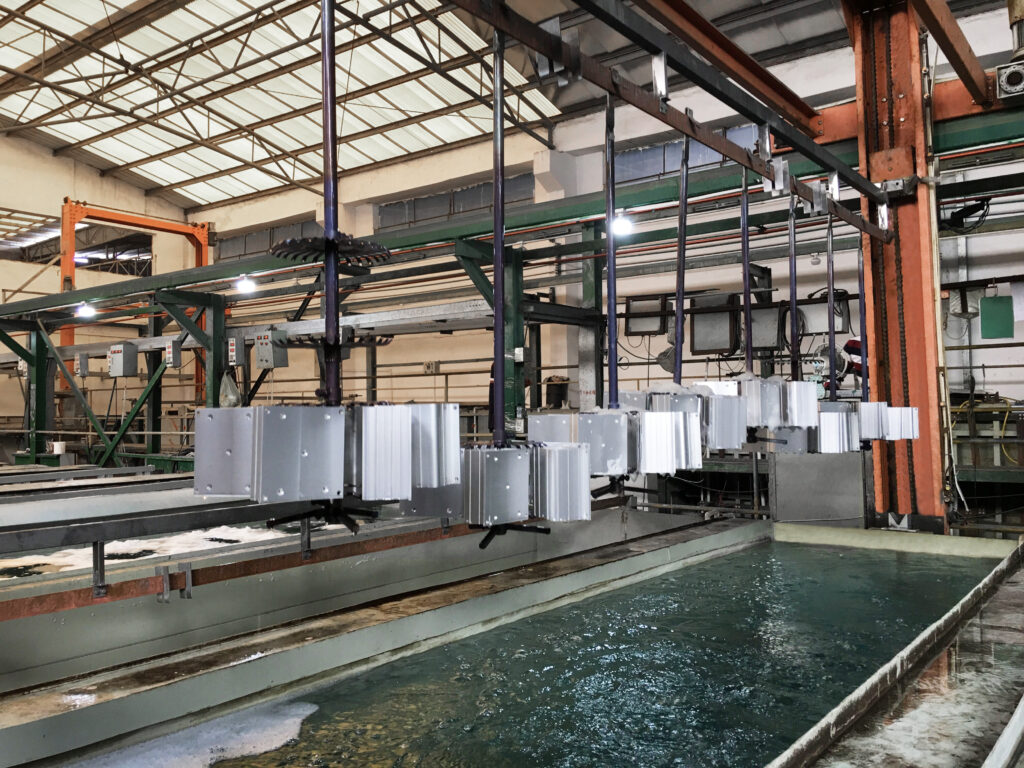
Should you anodize a heat sink?
Anodizing has been shown to improve the corrosion resistance, wear resistance, and convective heat transfer efficiency of extruded aluminum heat sinks. It also increases surface emissivity, which contributes to the efficiency of heatsink. Therefore, if you want to ensure your heatsinks will perform as expected, we recommend that you use a solution of hard anodized aluminum alloys to obtain desired effect in the shortest period. Of course, if you need to produce aluminum heatsinks in large quantities at a low cost, it is recommended that you should use one or two anodized finishes.
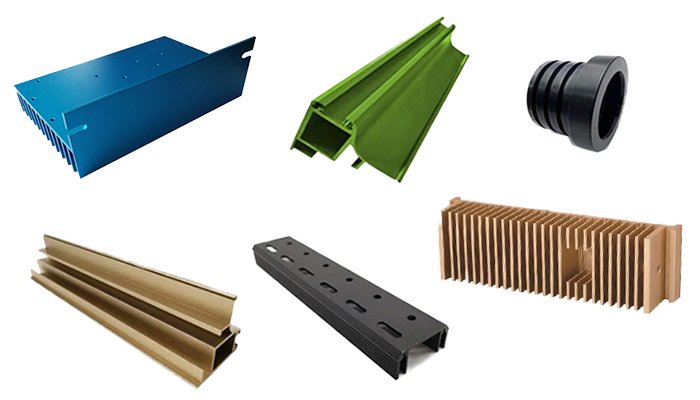
If you still have some doubts to anodize aluminum, you can consult Kaixin Aluminum, a professional aluminum heatsink processor, for more detailed customized heat sink solutions. Our technical engineers provide 24/7 technical support services covering CNC machining, metal stamping, surface finishes, and more for every customer!