CNC production cost represents the overall cost of manufacturing CNC parts during production. The unnecessary cost of CNC machining paid will cause a plummet in efficiency for CNC machining as well as product quality. Thus, Every enterprise sees reducing the undesirable cost of CNC machining as a crucial goal and pays more attention in CNC machining Process. Here are the following suggestions that teach the way for cost reduction during the machining processes.
Ways to reduce CNC machining costs for you
Site Visit
Before order confirmation, you should pay a visit to their factory for their production capacity and conduction, which is an effective way to avoid delayed delivery or substandard quality. Simultaneously, pay attention to their machine types. Additionally, you can also request CNC machined parts from the processor to check the technical level in all aspects.
Advance Planning
It’s good to deliver final products in a way that purchases raw materials and implements process planning. Based on past experience, long periods of delivery will increase the cost of CNC by over 25%. Conversely, Named as an expedited processing charge, additional charge should be paid as you want to receive products.
Choosing CNC Machines
Advanced CNC machine represents rapid production efficiency. For example, PIA-6500 and multi-axis CNC machines have been demonstrated to save machining time and manufacture a larger CNC part compared with CNC machining centers that only process individual pieces.
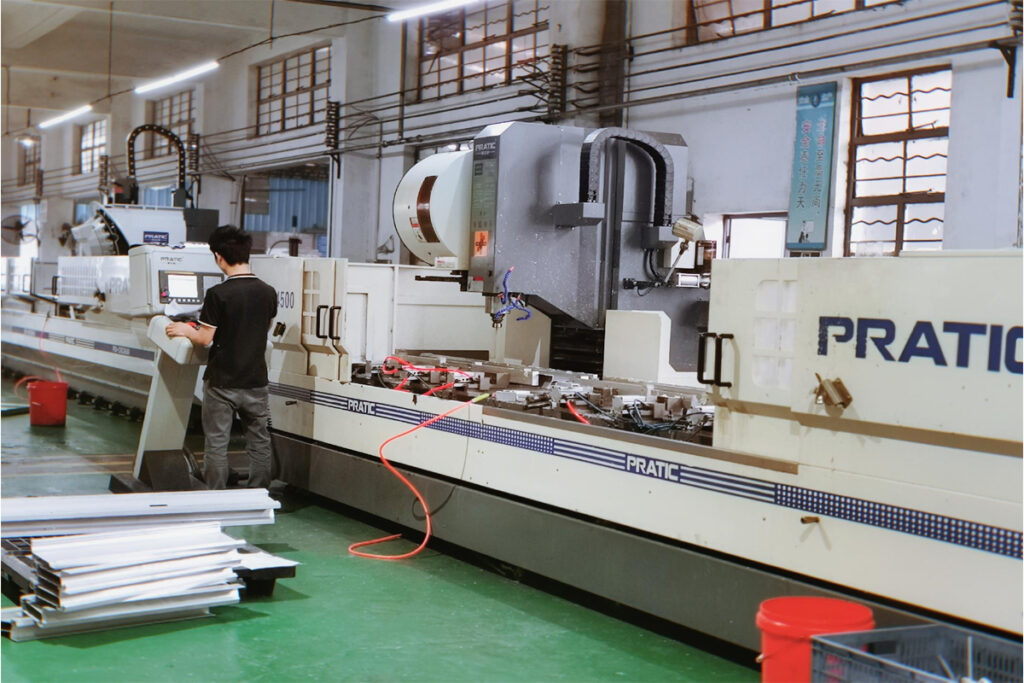
Customization Capability
Generally speaking, MOQ regulated by manufacturer is more than 50 Pcs. Negotiation permitted, you should avoid the subsequent cost caused by inconsistent mold specifications or quantities. Moreover, It is the same no matter how many Pcs you want to produce, which means mass production promotes allocation equitable.
Purchase Cost for Raw Materials
Generally, CNC manufacturer starts purchasing raw material for you after order confirmation. For some customers with special requirements, we also offer the following alternative solutions according to your budget.
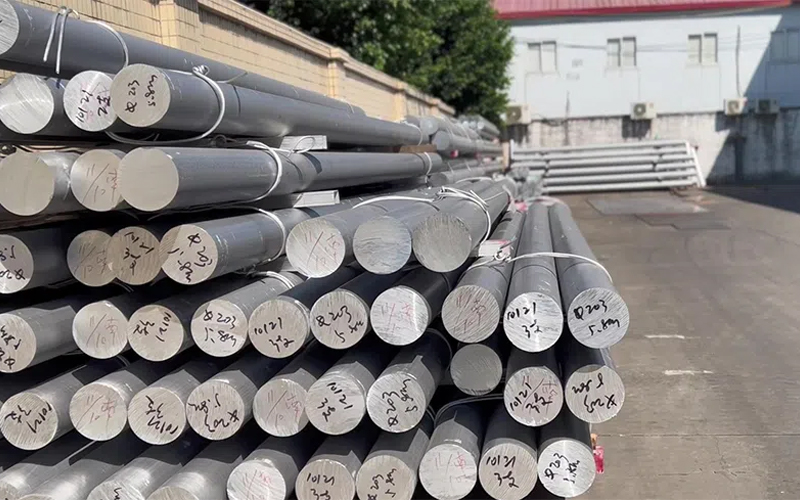
1, Delegating the purchase by partner of the manufacturer
CNC manufacturer will purchase material directly from long-term partner if you choose aluminum alloy with a low price. Then heatsink will deliver to CNC manufacturer after extrusion. At present, common softer materials are aluminum 6064, 6061, 7075, etc.
2, Delegating the purchase by others
Given that materials cannot purchase from partner, the CNC manufacturer will purchase material from another credible upstream supplier if you choose a copper-made heatsink with a high machining cost of CNC. But by the way, it can address the plight of the unknown prices offered by other suppliers when purchasing by yourself. Apart from that, save more time for yourself to operate your business well.
Ways to reduce CNC machining costs for manufacturing
Here are the following technical issues for CNC machining cost reduction. When placing order, below is several situations that argue manufacturer to improve CNC process.
Blank
Additional costs will be increased once the volume of blank material surpasses CNC machined parts. Since wasted material can not use for covering your cost, we recommend that volume of raw material should be no less than 3 mm.
Cutting Angle
Set with a specific program, CNC machine should be adjusted manually to 90° for cutting, causing an unnecessary cost for machining time——using large end mills are likely to overcut even under high-efficiency operating. Furthermore, using small cutting tool can enhance accuracy while increasing time for repetitive cutting. Anyway, here are the following measures for unit price:
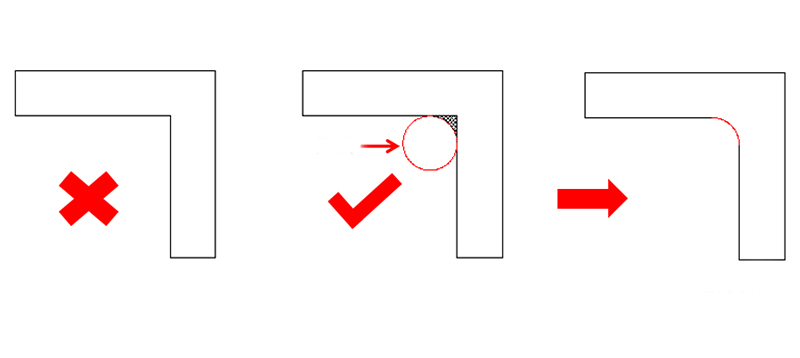
1, Rounding the edges of complex parts to ensure continuous operation.
2, Ensuring the ratio of the internal corner radii ranging from 3:1 (length: diameter)
3, All edges are machined to the same radius for avoiding frequent tool changes
4, Adding 5mm (or greater) rounded internal corners to ensure a faster cutting rate with CNC tools
Deep Internal Cavities
It’s crucial to choose a large end mill tool for processing deep pockets, which is no doubt you must spend more CNC machining cost for consuming more material and generating difficulty removing chips, leading to a profound impact for manual inspection. Besides, It will decrease the life of tool when manufacturing deep pockets, posing many issues such as tool chatter, wall chatter, tool deflection, etc. To avoid that, limit the depth by 2-3 times compared with parts diameter or adjust internal corners radius according to the regulation mentioned upon.
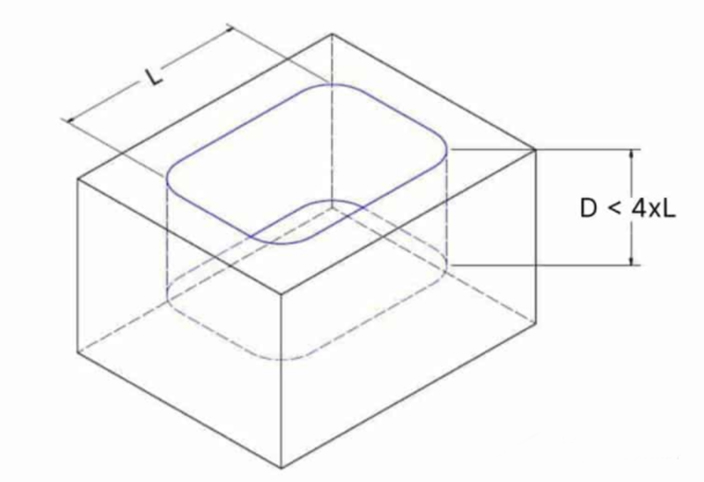
Tight Tolerances
You should control machine accurately to reduce the cost. But unfortunately, It’s complicated for CNC machining to achieve tight tolerance since there are burrs generating beside the fringe. Anyway, tight tolerances will increase the labor cost of manual inspection and CNC operators; the best way is to specify a standard tolerance that can meet the requirements of both parties.
Thin Walls
In most cases, it is best to avoid cutting thin walls because they are fragile and can be easily deformed or broken by machine vibration. On the other hand, CNC parts with overly thin walls are subject to ripples caused by machine vibrations that cause higher scrap rates. Especially in the complex vapour chamber heatsink which operates with lower machining speeds to avoid product scrap. Therefore, the minimum wall thickness is no less than 0.8mm. In addition, ask the processor to use sheet metal fabrication, which is a cost efficient process for thin wall.
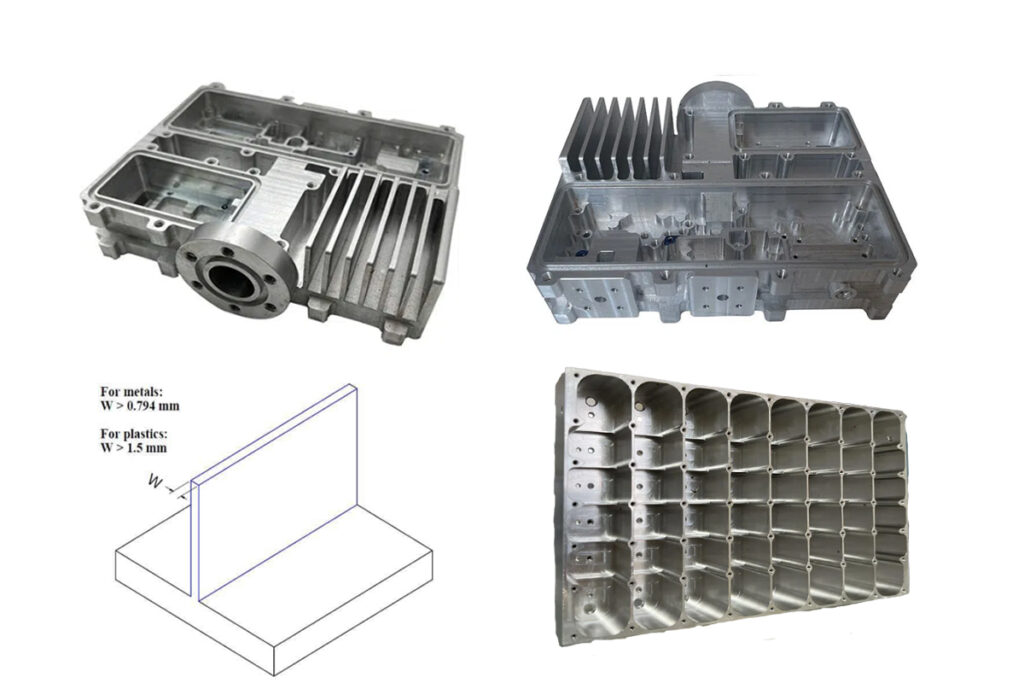
Limiting Thread Length
you should use special tooling to manufacture longer thread. But, over-standard threads will increase the production costs of CNC. To optimize CNC machined part, it is recommended to use threads with a maximum length of 3 times the diameter of the screw hole.
1, Thread Length: less than half the hole diameter (0.4-0.5 times)
2, Depth of Engagement: 4 times the diameter of the screw hole or 10 times of deeper machining holes、
Standard Drill Sizes
It is beneficial to reduce CNC machining costs in a way that is to leverage standard drill sizes. For special tools for CNC drilling, processors can arrange a plan quickly, and vice versa. In general, the more intricate the tool has, the more CNC machining time you should spend. For more information on how to measure the standard size of a CNC tool, please refer to the following information:
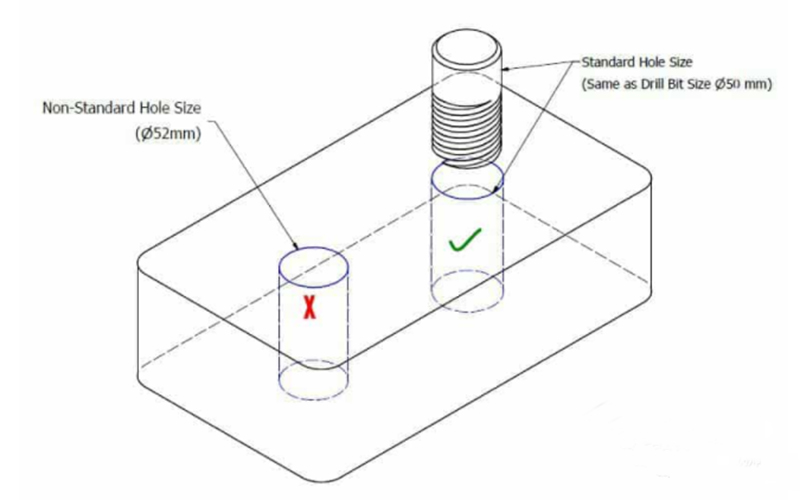
Avoiding Laser Engraving
Laser engraving is for small series only. Considering providing CNC products with engraving in a large volume in a short period, we recommend adopting powder coating or screen printing to greatly reduce the cost compared with CNC drilling, or just ignore these processing steps.
Avoiding Multiple Machine Setups
Some CNC machines do not involve automatic turning functions. Separately machined parts cause additional manufacturing costs. Therefore, it is important to minimize the number of workpiece flips and repositionings, which means put the same part into CNC machinery. For example, LED heatsink has a fixed position for drilling, so let’s take advantage.
Discrepant Height
To equip the heatsink into the machine, some heatsinks have different shapes such as high aspect ratio. the vibration of CNC machined parts will increase the unit price in manufacturing. To avoid time consuming, the aspect ratio of CNC part should be no more than 4 with adding support structure to enhance their rigidity.
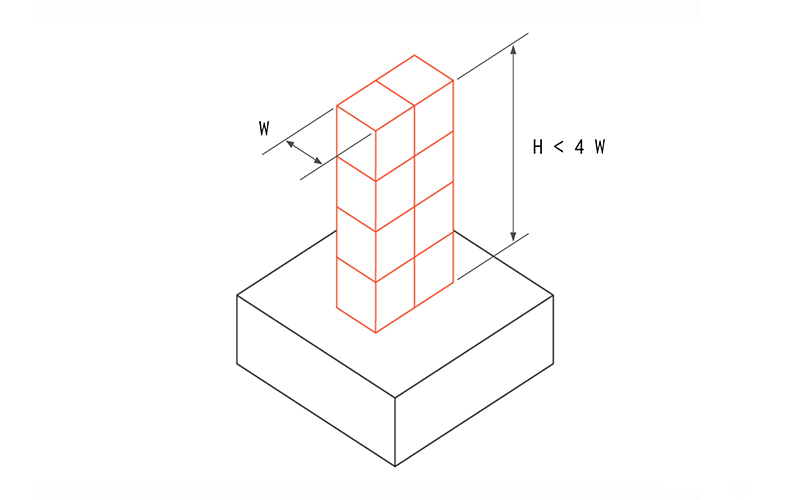
Finding A Reliable Heatsink Manufacturer
You can save money here and find a CNC machining with cost effective solutions With advanced design knowledge for CNC machining, Kaixin Aluminum strives to provide customized heatsink services ranging to varied processes for CNC machining and surface finishing including anodizing, electroplating, passivation, and metal stamping. Please let me know your requirement, and we will reply to you within 24 hours!