Are you list some good reasons to improve the accuracy of a CNC machine? This idea must be thought of when designing a CNC machine for manufacturing parts. It can certainly be said that the precise operation and accuracy of computer numerical control machines are very important. The article lists the different tools used in CNC cutting tools and explains their key functions. Understanding the functions of CNC machines is a crucial step in producing CNC parts by saving unnecessary costs.
What are the requirements for CNC cutting tools?
The CNC machie tools gift corrosion resistance to ensure the cutting tools maintain their excellent performance even after being scrbbed by cooling water. Because the cooling contains industrials alcohol, glycerin, and glycol chemicals that can react chemocally with air. High heat resistance is also crucial because the life of cutting tools is drastically reduced as the high temperature is generated by the CNC machine during high speed operation.
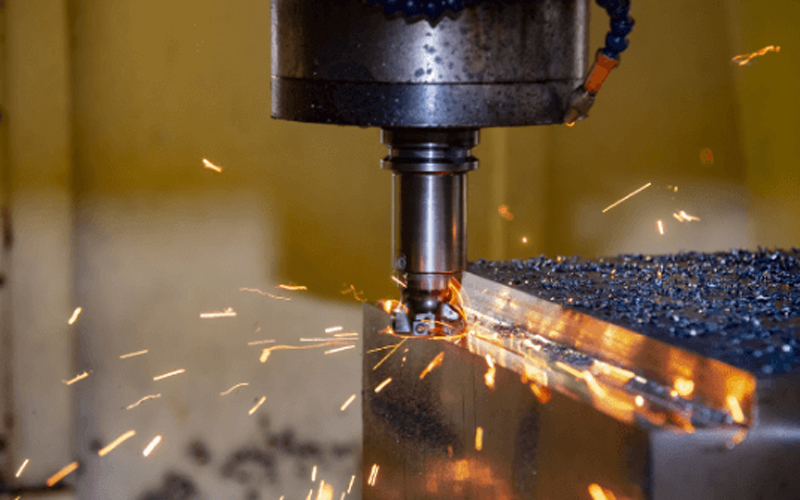
Generally speaking, CNC machining operations can generate temperatures up to 550°C without using cooling water. Furthermore, CNC milling tools need to be strong enough to withstand at least about 10,000 controlled cycles without losing their shape and characteristics. At the same time, the tools must be suitable for the mainstream types of CNC machines to reduce insert vibration or shedding during the machining process.
What materials can be used to make CNC cutting tools?
Carbon Steel
Carbon steel is a steel alloy containing up to 1% carbon and up to 1.6% manganese by weight. Due to its low cost and good cutting performance, carbon steel is the most popular CNC tool material for general CNC machining and is usually used to cut less hard metal materials such as aluminum, copper, and brass. However, carbon steel has a high hardness at room temperature after quenching and low-temperature tempering. But when the temperature is higher than 200 ℃, the hardness will drop sharply whereas its hardness has reduced to the original condition that is disabled to cut metal.
High Speed Steel
Mainly made of an alloy of carbon and tungsten, high speed steel tools (HSS) are most commonly used for machining harder materials such as stainless steel, titanium alloys, and hardened steel. Compared with carbon steel CNC tools, high speed steel tools still maintains a high hardness(Red Hardness) under high heat (about 500 ℃) with HRC 60. Due to its excellent characteristics, however, high speed steel is more expensive than carbon steel about three times.
Cemented Carbide
Called tungsten steel, it is an insoluble, high-hardness metal carbide particulate. Carbide tools are made of chromium tungsten and molybdenum and then fire under high temperatures and pressure conditions. With a high hardness (HRC75-80) and good wear resistance, carbide inside the alloy is more than HSS and it gifts a sound red-hard performance ranging from 800-100℃.
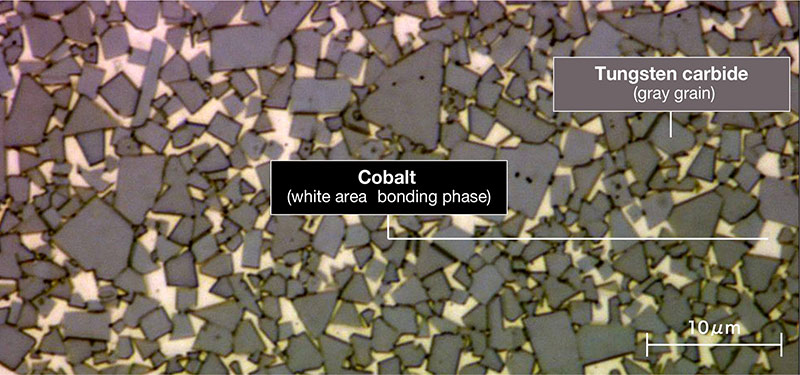
It is usually used to cut wear-resistant materials such as cast iron, non-ferrous metals, and alloy steel. However, price of cutting tool will be about 5 times than that of HSS with a weak impact against mechanical vibration. But it has excellent durability and cutting speed, which is suitable for the precise manufacturing process.
Ceramic
Compared to the above-mentioned materials, ceramic is the hardest material. End mill made of this material can cut through even harder metals such as titanium. The hardness of milling cutters is about HRC 90 with a melting point close to 2000°C, which is higher than the hardness of tungsten steel (HRC 90). However, their tool life is similar to that of carbide. Despite high hardness, ceramics are rarely used for manufacturing CNC machine tools as they are prone to cracking and chips. Apart from that, this cutting tool is also the most expensive of the materials mentioned above.
Common tool coating used in CNC machine tools
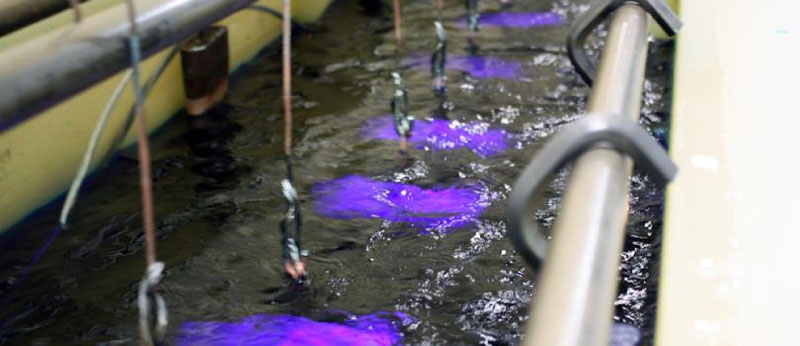
Titanium Nitride
Coated to less than 5 microns, titanium nitride coatings are effective in improving the life and wear resistance of CNC cutting tools and are commonly applied to carbide, HSS, and ceramic CNC machine tools. However, as CNC manufacturers have been working to improve production technology, titanium nitride is now being replaced by other coatings. As a result, it is not as widely used as it once was.
Super Life Titanium Nitride
Super life titanium nitride is a newer coating for CNC tools that is more durable than titanium nitride. It is commonly used on carbide, HSS and ceramic tools and effectively extends tool life up to 10 times longer compared to uncoated CNC tools.
Chromium Nitride
Considered as an improved titanium nitride coating, chromium nitride coating has better wear resistance, hardness, and lubricity. CNC tools with chromium nitride coating can stay sharp for a longer period of time compared to those with titanium nitride coating.
Aluminum Titanium Nitride(AlTiN)
This coating has an aluminum content of up to 65% and is used on CNC tools that require higher wear resistance. For example, CNC tools with AlTiN can keep their sharpness over 10 times longer than CNC tools without this coating when machining stainless steel and titanium alloys. Also, they are less likely to deform in high-temperature conditions. Additionally, studies have confirmed that the heat resistance is five times better than the original version.
Titanium Carbon Nitride(TiCN)
This coating is widely used in CNC machining for its excellent lubricity, hardness, and adhesion. CNC tools coated with TiCN enjoy excellent wear resistance and longer service life. CNC tools with TiCN coating can stay sharp up to 6 times longer than CNC tools without this coating. Moreover, they can cut harder materials such as diamond and titanium alloys.
Diamond-Like Carbon(DLC)
This is a higher-level CNC coating for CNC tools that need to cut hard materials such as stainless steel, Inconel, Hastalloy, etc. This coating has a lower coefficient of friction and adhesion than TiCN. Compared to the coatings mentioned above, DLC has a more expensive price—more than 10 times more expensive than TICN.
Cubic Boron Nitride(CBN)
CBN is chemically inert to iron, and steel under oxidizing conditions. they will form a thin layer of boron oxide when oxidized, providing chemical stability to the coating. Therefore, it has excellent heat resistance when machining hard iron and gray cast iron. Meanwhile, even though there is quite a high cutting temperature, it can cut heat-resistant steel, hardened steel, titanium alloy, etc.
Types and Functions of CNC Machining Tools
Since there are many types of CNC machine tools representing different processes, CNC cutting tool reduces the fatigue of CNC operators and machining time. CNC cutting tools are divided into various tools for drilling, turning, milling, and grinding. Among them, end mill is widely used in CNC machining tools:
Drill Bits
A drill cutter is a tool used in a CNC drilling machine for deep hole drilling. CNC drilling tools typically have two or more cutting edges that can drill many materials, including metals, wood, plastics, and composites. They are fast, accurate, and require little sharpening by the operator. Depending on the diameter and depth of existing holes, a variety of drill bits can be subdivided.
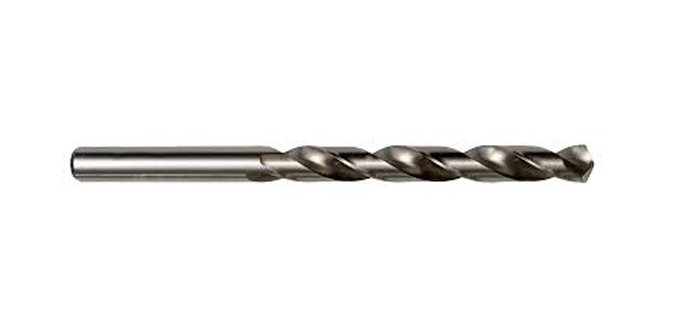
Twist Drill
Twist drills have one or more grooves, similar to an end mill. The most common twist drills are made of high speed steel (HSS) or solid carbide. A titanium nitride coating is also added to the surface to increase the hardness of the drill bit.
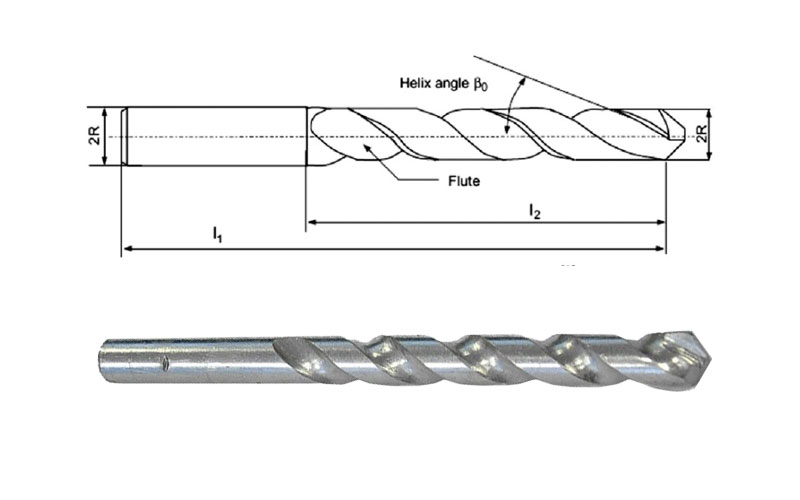
Center Spotting Drill bit
These stubby tools are used to create a pilot hole for the CNC drilling operation to provide a positional reference for the subsequent drilling process. Since the cutting edge is chamfered, the center drill is easily aligned with the workpiece.
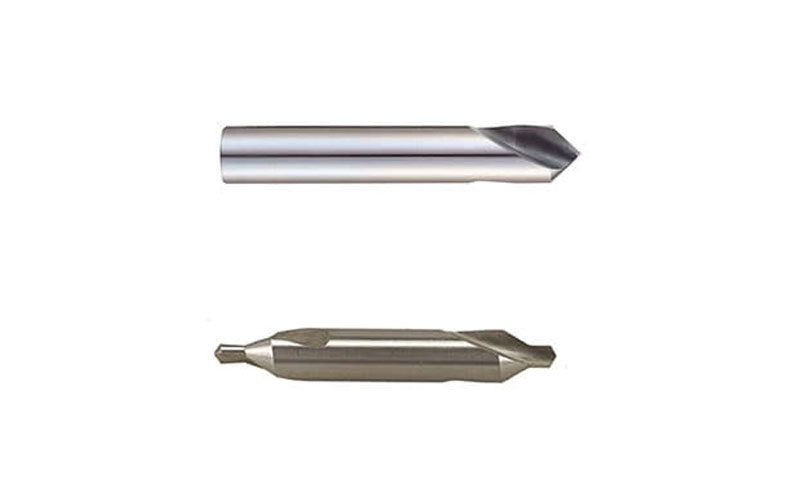
End Mill
These tool end mills are the most common in CNC machining CNC milling. They usually have up to eight flutes on different sides, allowing them to remove material in a short time. End mill is mainly used for cutting and milling CNC parts with slots, grooves, chamfers, and contour cutting, such as aluminum heatsinks. End mills can be classified according to the tip of the cutter:
Ball End Mill
Abbreviated as R-knives, they have a hemispherical tip for cutting various curved surfaces and parts with circular grooves. The tool is heat resistant and can withstand temperatures of 450-600°C. The conical cutting point allows easy penetration of CNC workpieces.
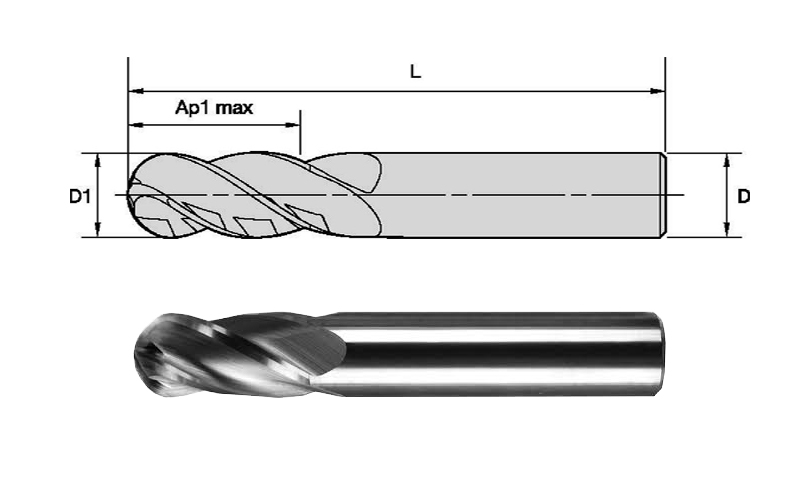
Flat End Mill
This is the most common CNC mill in milling machines. These CNC tools have a flat head with multiple slots and cutting edges that allow them to cut in all directions.
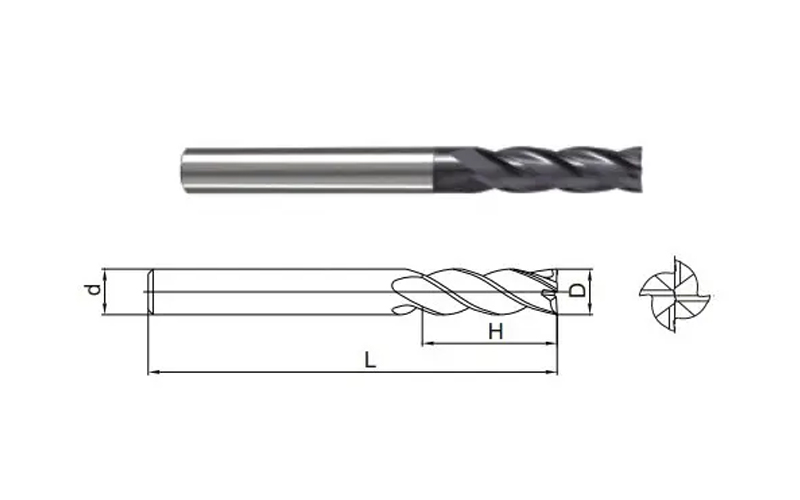
Thread End Mills
These tools are usually equipped with multi-axis thread mills to process internal or external threads for components. Compared to tapping, this tool is much cheaper than traditional process. In addition, the thread direction can be freely adjusted according to the program set by the thread mills, but tapping doesn’t make it.
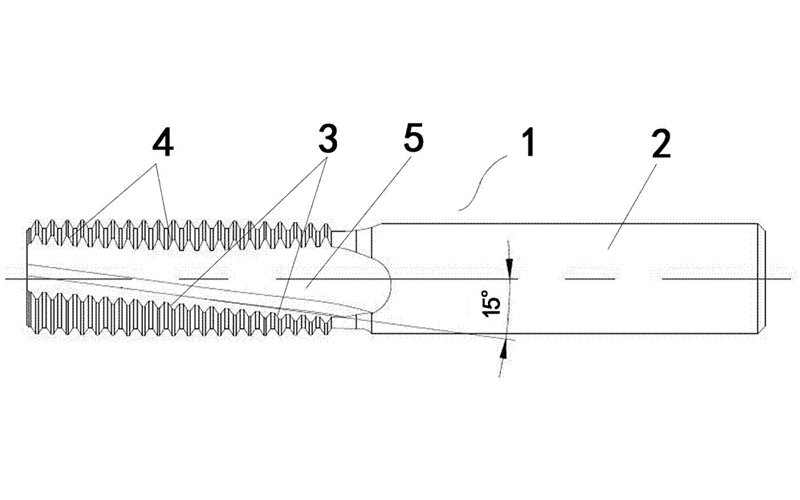
Slab End Mills
This type of tool is not commonly used in CNC lathes. The surface of the tool is machined with helical grooves for large-scale machining. And sometimes they are also used for surface grinding. This CNC machine tool is usually equipped for heavy machines in manufacturing industries.
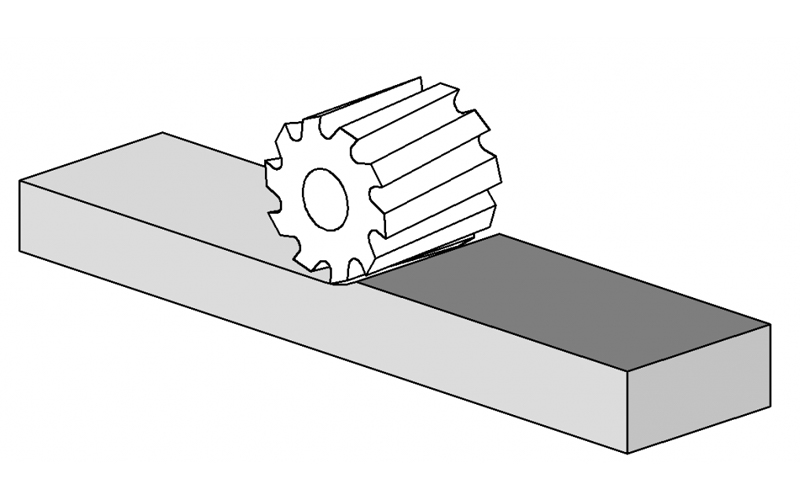
Face End Mills
This type of tool is used to mill flat surfaces. Since the cutting edge is located on the side of the milling cutter, only horizontal cuts can be made. The current face milling cutters can change the edge at will, which undoubtedly greatly extends working life compared to the old welded face milling cutters, where a broken blade would lead to the scrapping of the entire tool.
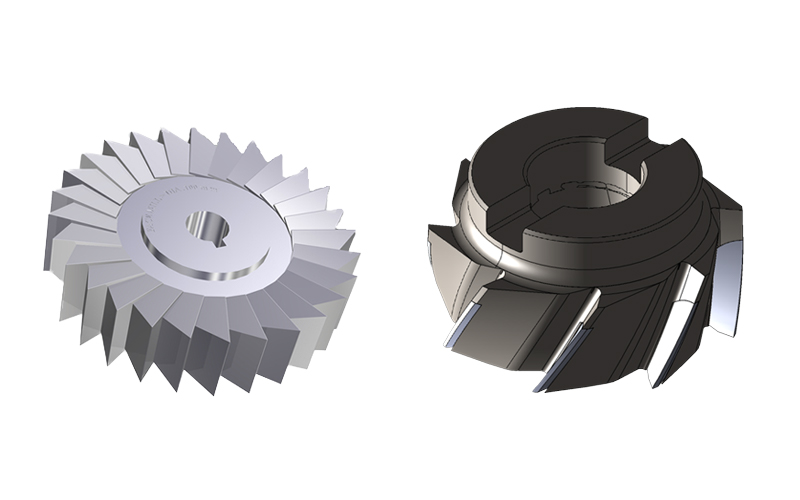
Involute Gear Cutters
These CNC machine tools are designed for involute gear machining, which can machine one or more flutes in a short time. Otherwise, it is difficult to machine using conventional methods. Of course, these gear cutters also have limitations – they can not cut all types of gears and may not be as accurate as other CNC cutting tools.
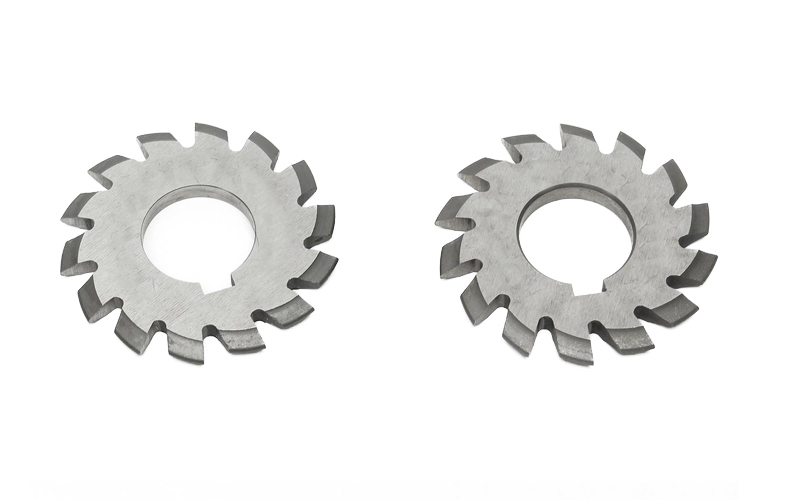
Roughing End Mills
Such end mills can increase cutting speed, which allows CNC machines to achieve higher productivity. However, in the pursuit of speed, the end mills sacrifice accuracy and leave a rough surface on the workpiece.
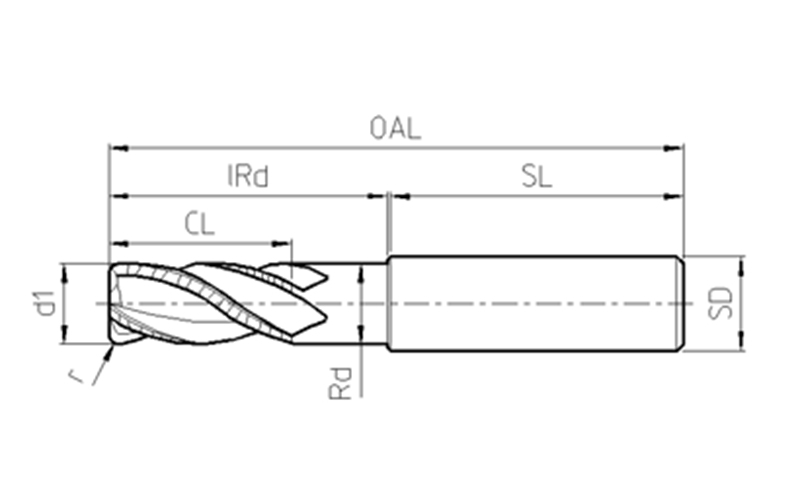
Hollow End Mills
Those types of CNC milling machines have pipe shaped cutting tools that can be used to make pockets and complex shapes in the material with different depths. This CNC tool has several advantages: longer cutting life, the ability to insert the surface with less force; better finishing quality. On the other hand, they are more difficult to handle with a low speed machining operation than many other CNC tools.
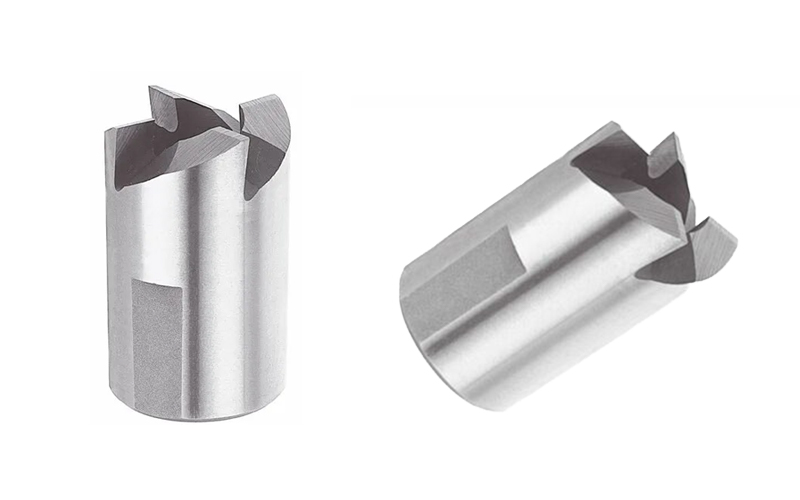
Side and Face Cutters
These tools have teeth on the sides and circumference and can be used to cut grooves and furrows. Milling cutters are also able to work at higher speeds than some other end mills, making them ideal for large projects. However, because of their size and shape, side and face cutters are likely to generate more mechanical vibration.
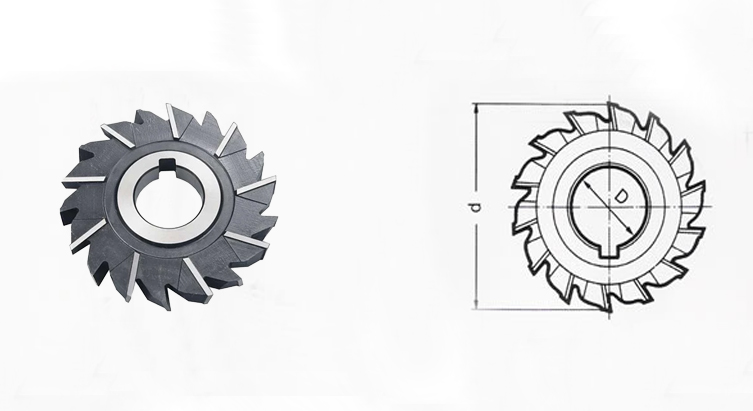
Other Tools
Turning Tool
Structurally, turning tools are divided into integral turning tools, welded assembly turning tools, and turning tools with mechanically clamped inserts. It is one of the most widely used tools in metal cutting, which can be used in CNC machine to process external circles, end planes, threads, internal holes, etc.
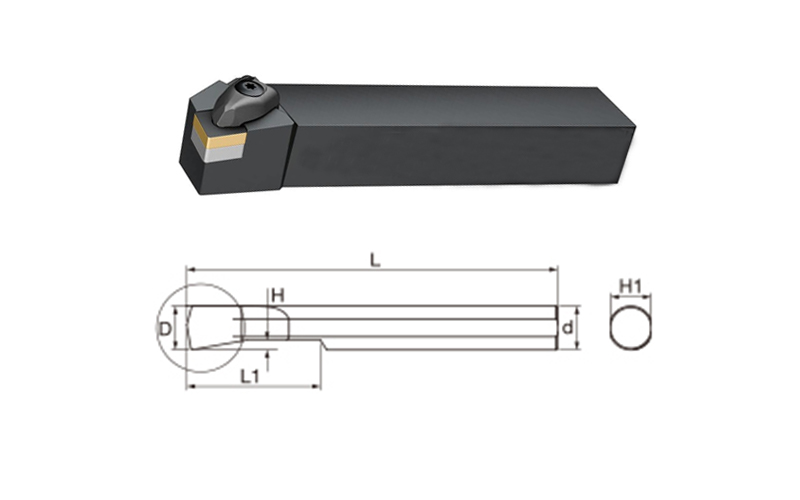
Reamers
These CNC tools can expand existing holes into a specific tolerance. They are suitable for the finishing and roughing machining process. They tend to provide a better surface finish than end mills and other CNC tools but are more expensive than other CNC tools.
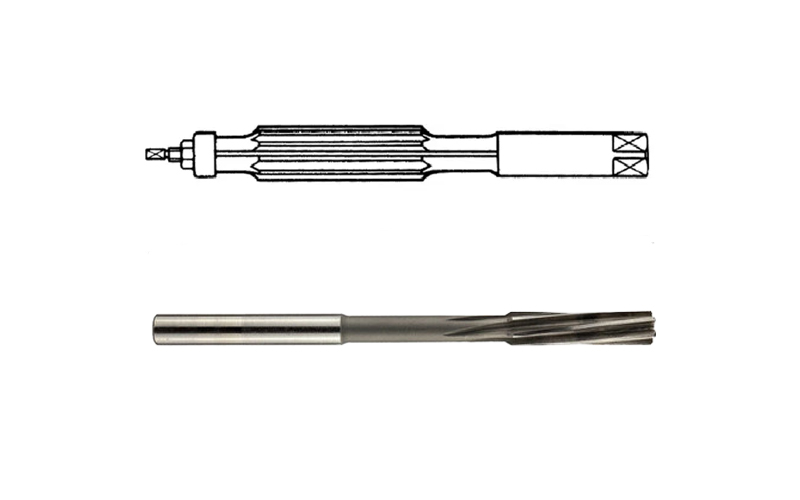
Fly Cutters
Flying cutters are cheaper face milling cutters. They consist of a main cutter body with one or two cutter heads attached to it. Fly cutters are CNC tools used for finishing and surface smoothing operations on CNC machines. At the same time, fly cutters have low speed operations with a smooth surface finish compared to other CNC tools.
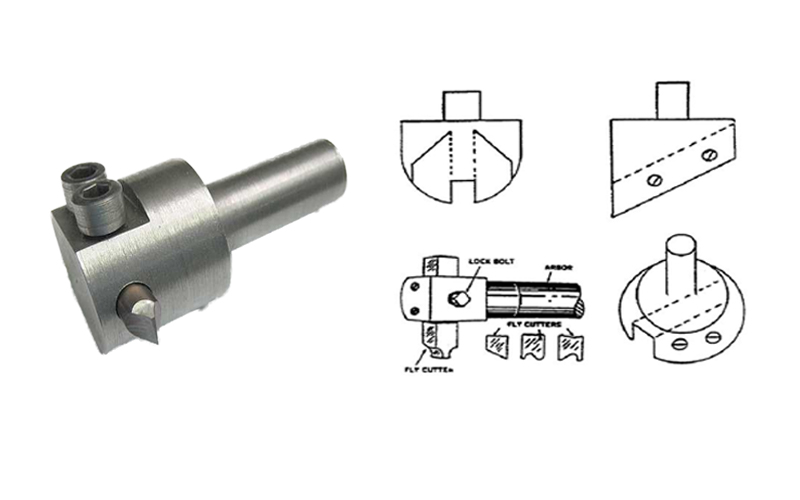
Taps
Tap is a tool for processing internal threads, which can be divided into varied taps for spiral groove, taper, straight groove, and pipe thread according to their shape. These tools are used for processing various medium and small size internal threads. Due to their simple structure and ease of use, tap tools are widely used in CNC processing.
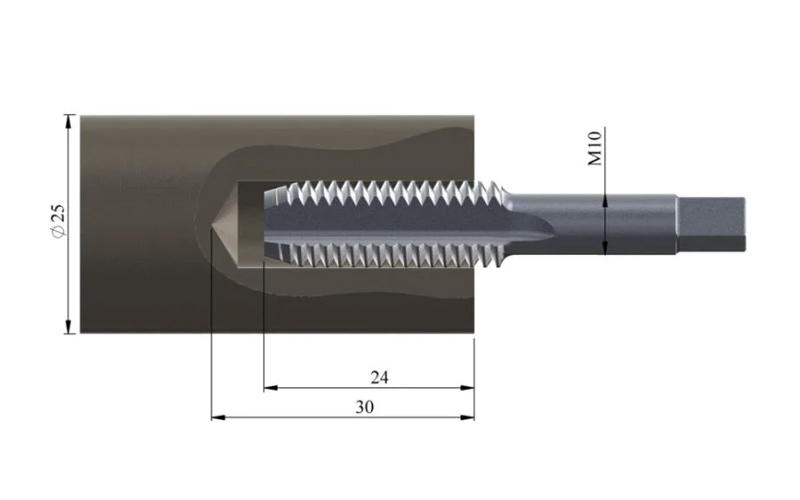
How to choose the right CNC machining – Kaixin Aluminum can help you
Extensive experience in aluminum fabrication is a very important factor that demonstrates a company’s credibility. When you entrust your job to Kaixin Aluminum, we are able to provide you with one-stop aluminum heatsink machining services with our 15 years of manufacturing experience. At present, our heat sink machining services cover CNC machining, metal stamping, and surface treatment.
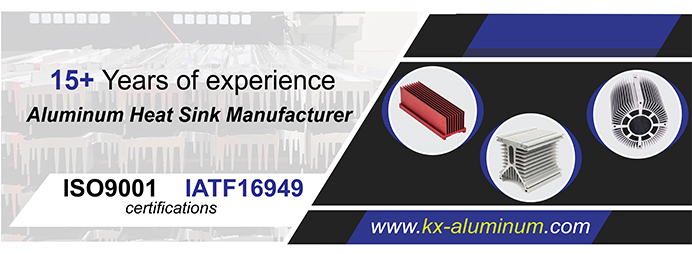
It is also important for us to maintain communication and technical support with our customers. We provide unparalleled technical support for every order. We provide 24/7 communication via email, phone, and our website. Contact us today to get started! We look forward to working with you!
FAQ
Q: In addition to tool selection, what other issues should I pay attention to in CNC machining?
A: Please check technical issues related to CNC machining.
Q: What is tool function in CNC?
A: CNC machines are computer numeric control tools designed to make accurate movements in a repeated pattern. During the 1940s and 50s, CNC cutting tools were introduced in the industrial world. These high-precision machines were used for various machining operations
Q: What is the qualified and right tool in CNC machines?
A: Right tool fits into a location on the machine, where its cutting edge is accurately positioned within close limits relative to a specified datum on the tool holder or slide.