Since natural metals are prone to wear, chemical corrosion, and environmental hazards, selecting a suitable surface treatment process is important to improve their performance. Surface treatments are designed to enhance the performance of metals in extreme environments. But how many types of surface treatments are there to choose from? Therefore, it is essential to understand the application of the surface treatment on the metal. In the longer term, surface treatment saves maintenance costs and increases production speed. In this article, we will explore the types of surface treatments and their different characteristics.
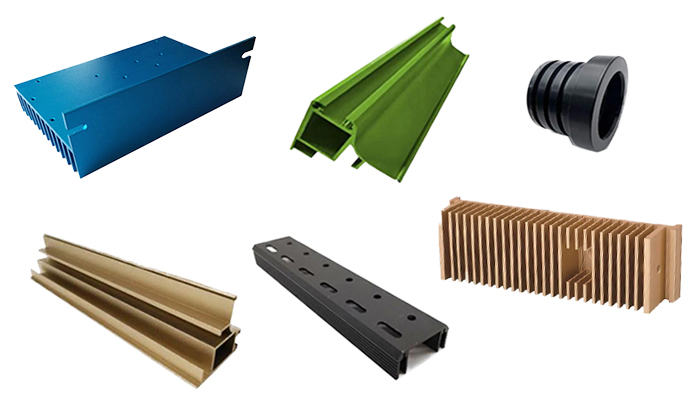
Why are surface treatments important?
As an important part of the manufacturing process, surface treatment is a process that changes the surface properties of metals, including painting, plating, anodizing, hardening, and coating, to make them suitable for varied applications. In this way, you will obtain the following advantages.
1) Enhancing Aesthetics – For furniture, a good look is more popular with consumers. In addition to preventing rust, gold anodizing brings out the premium look of the furniture; bronze anodizing brings a vintage look to the furniture; silver and white oxidizing is suitable for classic simplicity.
2) Improving Wear Resistance And Tarnish Resistance – The current hardening process can increase the hardness of the metal surface to over HRC50, which can greatly improve the wear resistance of metal products.
3) Corrosion Resistance – The metal surface generates a protective film through an electroplating process or anodizing, which can isolate between metal surface and surrounding to prevent chemical corrosion.
4) Enhancing Electrical And Thermal Conductivity – These electrical properties play a key role in electronic components, especially LED lights. You can control the junction temperature by reducing the heat generated by the electric current, thus ensuring that the LED light can function properly.
But anyway, Each type gifts its own edges. Before choosing the right surface finishing, you’d better make sure that the processing costs and the production cycle all are suited for your planning.
How many types of metal surface treatments are there?
Physical Surface Treatments
Polishing
Generally speaking, polishing refers to the process to get a smooth surface as a way that accesses cutting, material plastic deformation to remove the rough part. Currently, the common methods are divided into manual polishing and mechanical polishing, of which the former is equipped with sandpaper or wool wheel polishing wheel that press to the workpiece for obtaining a bright metal surface with 0.63 ~ 0.01μm.
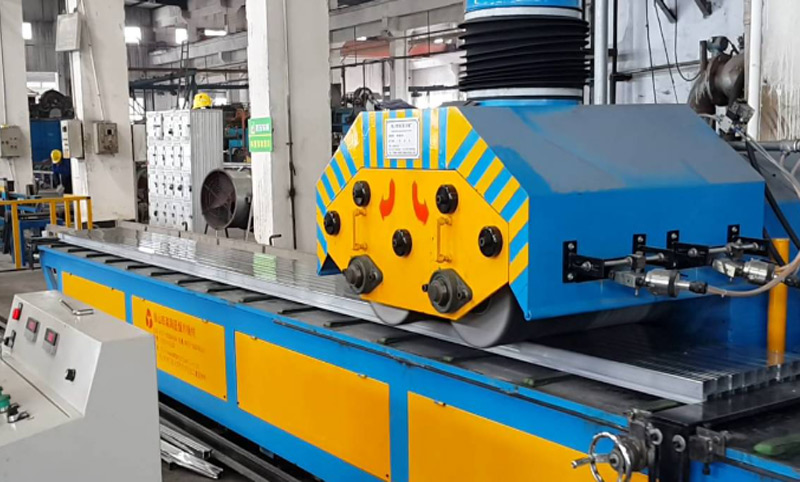
The latter uses a polishing machine to form a smooth surface with over 0.008μm through mechanical force, which can generate a glossy metallic surface compared to manual processing. Mechanical polishing is the most accurate method, which is suitable for polishing optical lenses.
Powder Coating
Spray painting is the most common surface treatment that is suitable for plastic or metals. Painting generally includes sandblasting, electrostatic painting, etc. Sandblasting is a surface treatment that mixes fine sand with other abrasives and blasts the grit onto metal surface by compressed air, which increases the wear resistance dramatically. In addition to fine grit, you can also choose between gravel or glass grit based on what kind of feel you want – rough or fine. Moreover, the mechanical properties of the surface are greatly improved due to the light cutting of the workpiece by the abrasive, which also increases the adhesion between the workpiece and the coating.
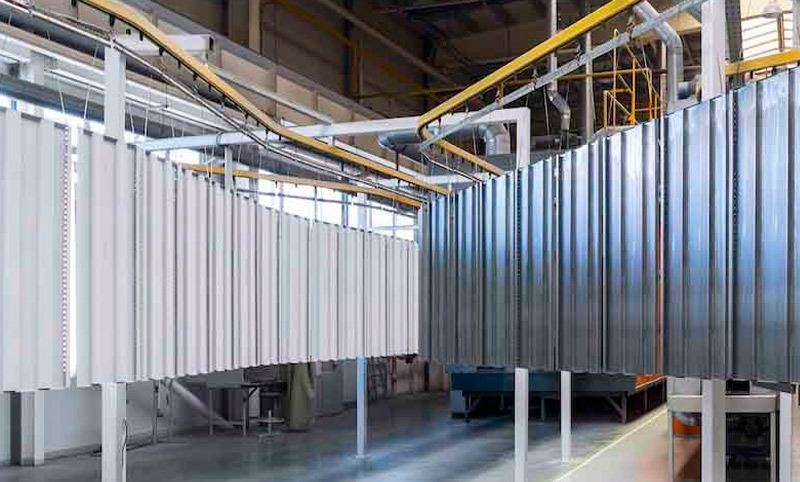
Electrostatic spraying is one of the processes in powder coating, where the paint is atomized by a spray gun and then applied evenly to the metal surface by electrostatic action. The advantage is that the paint can be easily distributed evenly and the surface is smoother than sandblasting, which improves heat dissipation of electronic components. However, this electrostatic spraying is costly as the process uses a large amount of flammable and toxic paint that is carried out in a working environment with more than 60 kV, which will be likely to generate electrical sparks as well as damage body health.
Hairline Surface Treatments
Unlike polishing, hairline finishing is a surface treatment process in which a line pattern is formed on the metal surface by grinding the product to form an aesthetic appearance. As surface hairline finishing enhance the metal feel, many people are favorable to using home appliance and mobile casing with hairline finishing.
There are two surface treatments for hairline finishing including straight hairline and messy hairline, of which the former is manufactured by a hairline machine to produce a uniformly distributed pattern; and messy hairline is manufactured by a non-woven or abrasive roller to produce a more diverse pattern.
Wood Grain Finishing
The wood grain treatment adopts the transfer method. With the help of electrostatic painting that provides a pattern on the aluminum surface, the osmosis membrane will be covered on the aluminum surface after applying vacuum. Finally, after heat treatment, the metal surface forms a same pattern.
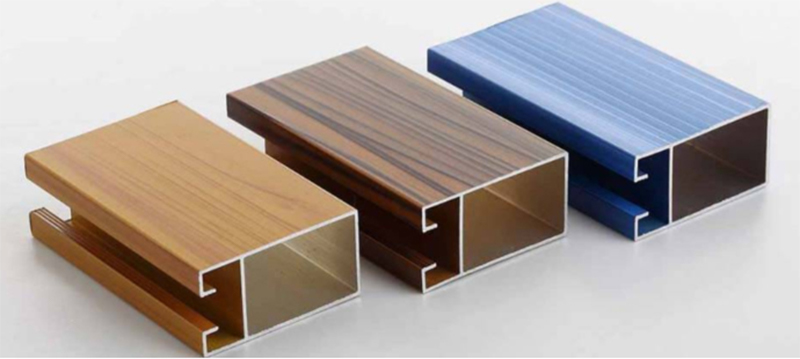
The advantage features simple processing, small investment, and low production cost in manufacturing, which is suitable for home appliances. Wood grain finishing is divided into mechanical abrasion and chemical dyeing processing, which both gift alternative metal coloring including white, black, brown, and brown. But mechanical abrasion method is more expensive than chemical dyeing finishing.
Chemical Surface Treatments
Anodic Oxidation
Anodizing is the most common surface treatment process that is to generate oxide films on the metal surface. With anodizing, you can anodize the metal to different metal coloring such as blue, green, gold, silver, and champagne.
There are three main types of anodic oxidation.
Type I anodizing: Mainly use chromic acid. This process produces non-conductive thin films with 0.08-0.25 um. Although this is the thinnest film in three anodizing types, these metal parts are often used for aerospace components or micro components. Furthermore, the protective layer feature gray or black metal parts as it can’t absorb dye. Moreover, liquid processing is more expensive than that of type II anodizing.
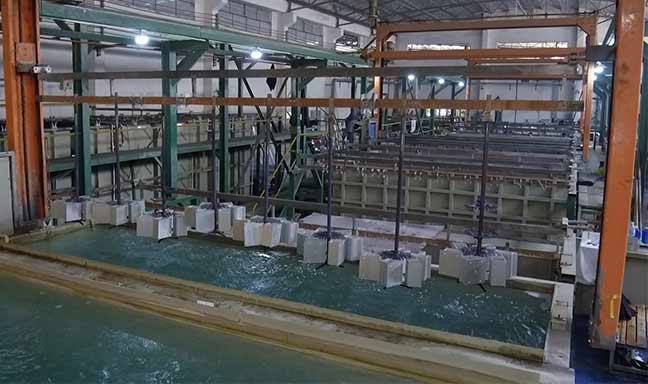
Type II Anodizing:Known as sulfuric acid oxidation, this surface finishing produces semi-conductive films with 2.5-25um, which means that the films can absorb more dye to generate a wide range of colors. This surface treatment process is widely used for construction materials, consumer electronics, optical components, etc. Moreover, sulfate ions are easily removed by chemical reaction with aluminum nitrate and magnesium hydroxide, which means cost of anodizing and waste management are cheaper than type I anodizing.
Type III Anodizing:Known as hard anodizing, this surface treatment uses a stronger electric current to produce thickest oxide film 12.7-80 um in three anodizing types, which means it gains a hardness of about 800 HV. Thanks to its outstanding corrosion protection, this surface treatment is mainly used in aerospace components, military, or larger structural objects. However, thick oxide film means it is not suitable for precision processing.
Electroplating
Electroplating is divided into aqueous plating and vacuum plating. Known as chemical coating, aqueous plating is a process in which metal parts are placed in a conductive plating solution to which ions are added to act as a reduction agent for attaching the metal parts. When applying electric current, the metal part will be treated as the cathode and the plating solution applies the electric current to form a thin metallic coating on the metal.
In contrast, vacuum plating is divided into vacuum evaporation plating and vacuum sputtering plating, where the former uses a tungsten wire as the electrode and melts the heated metals in a vacuum environment. Vacuum vapor deposition is divided into vacuum vapor deposition and vacuum sputtering. Vacuum sputtering, on the other hand, etches or coats metals by sputtering out atoms from the metal surface by impacting charged particles with high kinetic energy. This process is also known as vacuum vapor deposition.
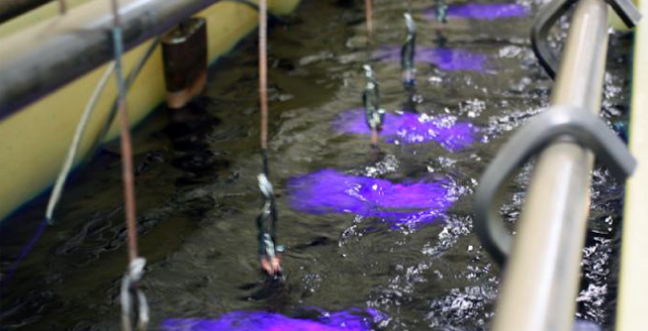
Compared to anodizing, electroplating surface treatment requires chemically inactive metals such as gold, nickel, and silver, which means that light metals such as aluminum are not suitable for electroplating because of the chemical reaction with the plating solution that produces aluminum salts and hydrogen gas. Although electroplating is to enhance high corrosion resistance for common metals, there are certain differences between each type.
Gold And Silver Plating:mainly used for decoration but pricey.
Nickel Plating:Featuring the most common plating process, the metal is chemically stable in the atmosphere and alkaline solution – not easily discolored.
Chrome Plating: Expensive material with good hardness and high temperature resistance, but easy to crack at low temperatures.
Tin Plating:Own a stable chemical property, and does not dissolve in dilute solutions such as sulfuric acid, nitric acid, hydrochloric acid, etc.
Galvanized:Low cost and easy processing, which is used to prevent internal metal rust. However, the disadvantage is not wear-resistant.
Passivation
Chemically active metals such as aluminum are treated by immersing them in an acidic solution, such as nitric or sulfuric acid. This process forms a thin protective film (often transparent) on the surface of the metal to reduce the chemical activity, i.e. you can interpret this as a surface treatment process that turns the active metal into a precious metal.
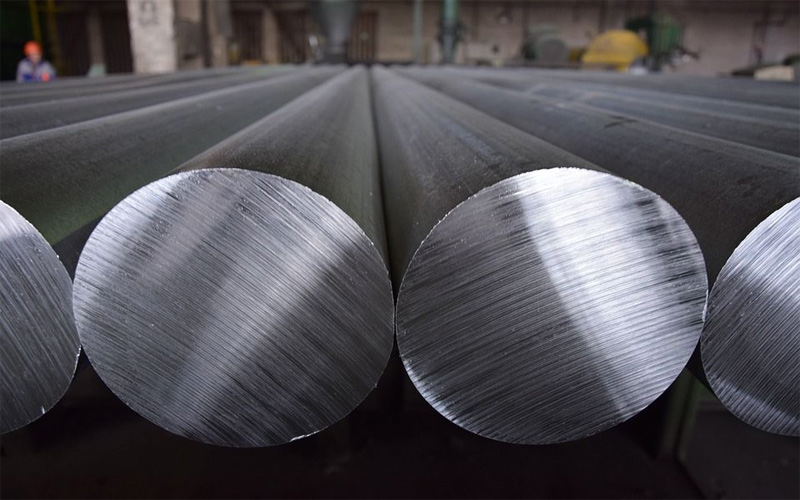
The passivation process is divided into chemical passivation and pickling passivation, where the former is a passivation produced by the natural reaction between the metal and the passivating agent. For example, metals such as chromium, aluminum, and titanium are easily passivated in oxygen-containing solutions, so these metals also become self-passivating metals. In this way, the corrosion rate can be slowed down dramatically; the other passivation process is to remove oil, rust, and other dirt. After the treatment, the surface will become silvery white and it greatly improves the corrosion resistance.
Nitride Surface Treatment
Nitriding process is divided into hard nitriding and nitrocarburizing, where hard nitriding, also known as nitriding, is a chemical heat treatment process that infiltrates nitrogen atoms into the metal layer. Ammonia decomposes nitrogen atoms at high temperatures of 500-600 ℃ to form a nitriding alloy, thus changing the mechanical and chemical properties of the metal.
Named carbonitriding, nitrocarburizing is a thermal surface treatment process by infiltrating carbon and nitrogen into the metal surface. Compared to hard nitriding, this surface treatment gifts a faster depth, tempering, and corrosion resistance, as well as excellent wear resistance. Due to the low processing temperature (usually 200-400 ℃), this surface treatment will replace the nitriding process in the future.
Consult a professional before deciding on a surface treatment processes
Kaixin Aluminum is a credited Chinese manufacturer for manufacturing heatsinks. We provide varied manufacturing processes such as surface treatment, CNC machining, metal fabrication, etc.
We have established a responsible QC team and sophisticated engineering team paying great attention to product quality and offering technical support to our strategic partners. As our product quality is primarily customer-driven, we not only can provide our customers with high-quality heat sinks but also innovative and cost-effective thermal solution for our clients to meet the increasingly diversified heat sinks market demand.